Lösungen und Branchen
Die Kombination aus hervorragenden Materialeigenschaften und einem hoch effizienten Produktionsprozess, erlaubt uns die Verwendung von Sitomb in einer Vielzahl von Industrien.
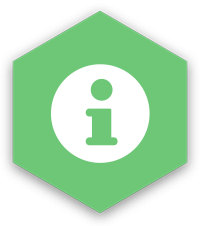
Wo verwendet man Sitomb®?
Eine starke Legierung
Werkstücke, die aus Sitomb gefertigt werden, ermöglichen viel Freiheit beim Design und dem Produktionsprozess. Aus diesem Grund können wir fast alle Kundenvoraussetzungen erfüllen. Eine Vielzahl von Produkten kann somit realisiert werden. Unsere Erzeugnisse beginnen ab einem Gewicht von wenigen Gramm und enden bei Produkten von bis zu 10 kg. Zudem erreichen wir exzellente chemische und mechanische Eigenschaften. Verschiedene Geschäftsbereiche, wie die Schloss- und Beschlagindustrie, die Automobilindustrie, die Medizintechnik, der Maschinenbau sowie die Luft- und Raumfahrtindustrie profitieren von Sitomb.
Kostengünstige Produktion
Teile aus Siliziumtombak werden im Druckgussverfahren hergestellt und können daher ab einer Losgröße von 1000 Stück hoch profitabel hergestellt werden. Ein wesentliches Element in diesem Prozess ist, dass wir permanente Gießformen anbieten. Sie werden auf Basis des gewünschten Endprodukts hergestellt. Durch unsere permanenten Gießformen, startet erst die eigentliche Produktion mit unseren Druckgussmaschinen.
Der als „Schuss“ bezeichnete Produktionszyklus besteht aus den folgenden Schritten: Füllen der geschlossenen Form, Abkühlen, Spannen und endgültiges Öffnen der Form, wodurch das Endprodukt entsteht. Normalerweise muss das Produkt danach vom überschüssigen Material befreit werden und ist dann fertig. Weitere Schritte zur Anpassung der Geometrie und / oder der Oberfläche des Bauteils sind problemlos möglich.