Beschaffung von hochfesten und präzisen Bauteilen
Eine Entscheidungshilfe für Konstrukteure und technisch orientierte Einkäufer.
Für die Beschaffung von hochfesten und präzisen Bauteilen kommen in der Regel die folgenden Fertigungsverfahren in Frage:
- Feinguss – Investment Casting
- Metal Injection Moulding (MIM) – Metallpulverspritzgießen
- Druckguss – High Pressure Die Casting
- Sandguss – Sand Casting
Jetzt kostenlose Konstruktionsrichtlinie runterladen!
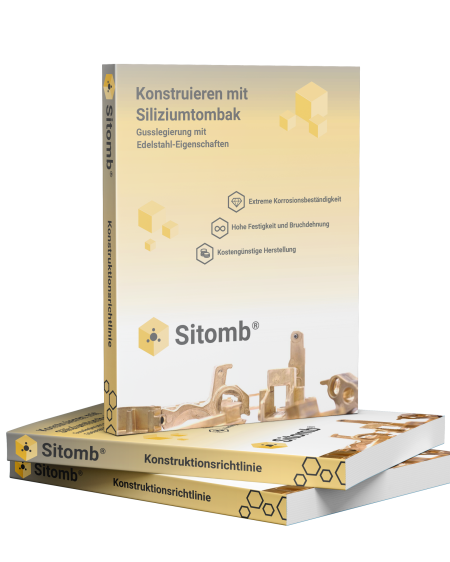
Feinguss, Druckguss und Sandguss sind der Herstellungskategorie „Gießen“ zuzuordnen. In der Gießereitechnik kann wiederum zwischen zwei Hauptgruppen an Gießverfahren unterschieden werden.
Gießen in verlorene Formen:
Bei den verlorenen Formen sind insbesondere das Sandgussverfahren und das Feingussverfahren zu nennen. Nach der Erstarrung des Gussteils im Formhohlraum werden die Formen zerstört, um das Gussteil entnehmen zu können. Weil die Formherstellung in jedem einzelnen Gießzyklus integriert ist, sind diese Verfahren tendenziell aufwendig und wenig prozesssicher (daher auch nicht automatisierbar).
Gießen in Dauerformen:
Der Druckgussprozess hingegen ist dem Gießen mit Dauerformen zuzuordnen. Die Formherstellung ist hier nicht Bestandteil des Gießzykluses. Es wird immer wieder in die gleiche Form aus Werkzeugstahl gegossen. Die Prozesssicherheit, als Grundlage für Automatisierbarkeit und reproduzierbare Qualität, wird durch das Gießen in die immer gleiche Form deutlich erhöht.
In Abgrenzung zu den Gießverfahren handelt es sich beim MIM-Verfahren nicht um einen Gießprozess, sondern um ein Sinterverfahren.
Beim Druckguss muss die Festigkeit des verarbeiteten Materials berücksichtigt werden. Zinkdruckguss und Aluminiumdruckguss sind häufig nicht fest genug. Legierungen auf Kupferbasis, wie bspw. Siliziumtombak, weisen ähnliche Festigkeitseigenschaften wie Bauteile auf Fe-Basis auf und können somit eine echte Alternative zu Feinguss und MIM darstellen.
In einem Grenzbereich vermag auch Sandguss die geforderten Eigenschaften zu erfüllen, wobei Sandgussbauteile in den meisten Fällen nicht die geforderte Oberflächengüte und Toleranzgenauigkeit liefern.
Im Folgenden sind die charakteristischen Merkmale der vier Herstellungsverfahren gegenüber gestellt. Es werden Vor- und Nachteile herausgearbeitet. Anschließend wird ein Fazit gezogen.
Verfahren
Das Feingießen oder auch Wachsausschmelzgießen, zählt zu den urformenden Verfahren mit verlorenem Modell und verlorener Form.
Die verlorene Form besteht aus Keramik und ist dadurch gekennzeichnet, dass sie nach jedem Abguss zerstört wird, um das Gussteil entformen zu können. Die Gussform geht also nach jedem Gießzyklus „verloren“.
Zur Herstellung der verlorenen Formen wird zusätzlich ein verlorenes Modell aus Wachs oder Polymer benötigt.
Das Feingussverfahren wird zur Herstellung von Gussteilen eingesetzt, an die Anforderungen wie eine hohe Oberflächengüte und eine ausreichende Form- und Maßtreue gestellt werden.
Als Basiswerkstoff kann dabei jede Metalllegierung, dessen Fließeigenschaften im flüssigen Zustand zur homogenen Füllung der keramischen Form ausreicht, eingesetzt werden. Sehr häufig wird Stahl oder Edelstahl verwendet, wodurch die geläufige Bezeichnung Stahlfeinguss oder Edelstahlfeinguss geprägt wurde. Für die Fertigung der keramischen Form werden zunächst Modelle aus Polymer oder Wachs benötigt.
Diese werden bspw. auf einer Spritzgießmachine hergestellt und entsprechen der Form der gewünschten Werkstücke aus Metall (Positivmodell). Da in der Regel in einem Zyklus mehrere Werkstücke gegossen werden, werden die Wachs- bzw. Polymermodelle an ein Speisersystem (Gusstraube) angebunden. Als nächstes wird die Gusstraube in ein Bad mit einem so genannten Schlicker eingetaucht und anschließend besandet. Dieser Vorgang wird zyklisch solange wiederholt, bis die keramische Schicht die notwendige Dicke erreicht hat.
Nun muss die keramische Form von den eingeschlossenen Modellen befreit werden. Dazu werden die Formen in einem Autoklav-Ofen erwärmt, sodass der niederschmelzende Modellwerkstoff aufschmelzen und auslaufen kann. (Andere Werkstoffe, wie etwa aufgeschäumtes Polystyrol kann durch direktes Eingießen der metallischen Schmelze entfernt werden – Achtung: Gasbildung kann zu Qualitätsnachteilen führen.)
Nach dem Entfernen des flüssigen Modellwerkstoffs findet das Brennen der keramischen Formen bei über 1000°C statt. In die noch warme Form wird im Anschluss die flüssige Metallschmelze gegossen. Dieser Prozessschritt wird händisch durchgeführt. Der flüssige Werkstoff kühlt nun in der Form ab und nimmt die gewünschte Gestalt an. Nach dem Erkalten muss die keramische Form zerschlagen werden um die Werkstücke freilegen zu können. Die Werkstücke werden dann von der Traube abgesägt und die Stelle des Angusses wird anschließend überschliffen.
Im Folgenden ist der Ablauf des Feingussverfahrens skizziert:
- Schritt 1: Verlorene Wachsmodelle (Positivmodelle) herstellen. Für mittlere bis große Stückzahlen erfolgt dies in der Regel über ein Spritzgussprozess:
- 1.1 Form schließen
- 1.2 Kunststoff wird in Extruderschnecke aufgeschmolzen, Extruderschnecke fährt vor und füllt die Kavität
- 1.3 Erstarrung, Form öffnen
- 1.4 Entnahme des Gussbaums (Angusssystem und Gussteile)
- 1.5 Aufbringung von Formschlichte
- 1.6 Trennen der Wachsmodelle vom Anguss
- Schritt 2: Wachsmodelle händisch zu einer Modelltraube fügen (Wachsmodelle werden mittels Lötkolben an ein Angießsystem aus Wachs angeschmolzen)
- Schritt 3: Wachs in Keramikschlicker tauchen, erste Schicht trocknen lassen
- Schritt 4: Berieseln mit Sand, wieder in Keramikschlicker tauchen, zyklisches Tauchen und Berieseln (ca. 10-mal)
- Schritt 5: Brennen der Keramikschale, dabei wird der Wachs ausgeschmolzen
- Schritt 6: Gießen des Metalls in die glühende Keramikform
- Schritt 7: Abkühlen lassen (mehrere Stunden)
- Schritt 8: Keramikschale zerstören, Gussbaumentnahme
- Schritt 9: Keramikbruchstücke entsorgen
- Schritt 10: Aufwendiges Trennen der dicken Anschnitte mittels Trennscheibe. Dadurch dass nur der Druck der Schwerkraft zur Formfüllung genutzt wird, sind dicke Anschnitte notwendig. Anschließend händisches Überschleifen der Anschnitte
- Schritt 11: Reinigung des Gussteils von Rückständen der Keramikschale
Vorteile des Feingussverfahrens
- Gut geeignet für Bauteile mit extrem hoher Komplexität
- Near-net-shape Produktion, d.h. endkonturnahe Produktion
- Werkstücke unter einem Gramm bis 100 Kilogramm realisierbar
- Breites Spektrum an metallischen Werkstoffen kann verarbeitet werden
Nachteile des Feingussverfahrens
- Automatisierung nicht möglich, Verfahren mit viel Handarbeit.
- Lange Prozesskette, lange Zykluszeit
- Viel Abfall durch das Arbeiten mit verlorenen Formen und verlorenen Modellen
- Schwankungen der Maße im Produktionsprozess, da für jedes Gussteil ein neues Modell und eine neue Gussform angefertigt werden muss
Die Recyclingfähigkeit im Herstellungsprozess ist durch die verlorene Form und das verlorene Modell stark eingeschränkt. Es tritt sehr viel Verschwendung auf, was zum einen aus umwelttechnischen Gründen nachteilig ist und zu anderen auch nicht dem Lean-Gedanken „Vermeidung von Verschwendung“ moderner Fertigungsbetriebe entspricht.
Stark ist das Feingussverfahren vor allem für extrem komplexe Bauteile mit zahlreichen Hinterschneidungen, die sich im Druckgussverfahren nicht herstellen lassen. Außerdem kann das Feingussverfahren bei sehr kleinen Stückzahlen wirtschaftlich vorteilhaft sein.
Wenn der Werkstoff Stahl ein Muss ist, kann ebenfalls nicht auf Feinguss verzichtet werden, da die Verarbeitung von Stahl im Druckgussverfahren nicht möglich ist. Denn in diesem Fall würde Stahl in Stahl gegossen werden. Dies würde dafür sorgen, dass die Metallform extrem schnell verschleißen würde. Als Alternative für Edelstahl wird oftmals Siliziumtombak eingesetzt. Der Vorteil dieses Werkstoffs ist, dass er ähnliche Eigenschaften wie Edelstahl aufweist, jedoch trotzdem im Druckgussverfahren verarbeitet werden kann. Die wirtschaftlichen und prozesstechnischen Nachteile des Feingussverfahrens können so umgangen werden.
Das Metal Injection Moulding Verfahren lässt sich mit den anderen hier dargestellten Verfahren nur bedingt vergleichen – es handelt sich nämlich nicht um ein Gussverfahren. Die finalen Bauteileigenschaften werden über einen Sinterprozess eingestellt.
Das Grundmaterial für das Verfahren ist ein Gemisch aus Metallpulver und einem Binder auf Polymerbasis, welches zu einem sog. Feedstock aufgearbeitet wird. Für das eigentliche Formgebungsverfahren wird das pelletierte oder granulierte Gemisch in eine Spritzgießmaschine gefüllt. Dort wird es durch einen doppelten Schneckengetrieb gefördert, erwärmt und verdichtet. Dadurch schmilzt der Binderanteil des Gemischs auf, es bildet sich eine zähflüssige Masse mit Metallpartikeln, die anschließend in die Spritzgussform geschossen wird. Nach dem Schuss erkaltet das Polymer und es wird ein instabiler Grünling aus dem Werkzeug ausgeworfen.
Dem Grünling muss nun der Binder entzogen werden. Dies geschieht, je nach Art des Binders, in einem Ofen oder einem Lösungsbad. Die inzwischen gängigste Weise ist die Lösung im Ofen, sodass der Grünling für den nächsten Prozessschritt, dem Sintern, nicht zusätzlich bewegt werden muss und lediglich die Parameter des Ofens angepasst werden müssen. Infolge des Sinterns werden letzte Bindemittelreste entfernt und das Werkstück erhält seine endgültige Form und mechanische Eigenschaften. Erst durch das Sintern werden die Metallpulverpartikel des Bauteils verbunden.
Im Folgenden ist der Ablauf des MIM-Verfahrens skizziert:
- Schritt 1: Mischen von Metallpulver und Binder
- Schritt 2: Feedstockherstellung durch Granulieren der Mischung
- Schritt 3: Einfüllen des Feedstocks in eine Spritzgießmaschine
- Schritt 4: Feedstock wird in die metallische Dauerform eingespritzt
- Schritt 5: Form öffnen und Entnahme des sog. Grünlings
- Schritt 6: Abtrennen der Anspritzpunkte
- Schritt 7: Vorsichtiger Transport zur Entbinderanlage
- Schritt 8: Sinterprozess: benötigt hohe Temperatur (> 1000°C für Fe-Basis Bauteile), lange Zeit (>24h) und häufig Druckunterstützung
- Schritt 9: Abkühlen des Bauteils
- Schritt 10: Korrektur des Verzugs bedingt durch die Schrumpfung des Grünlings zum Fertigteil
Vorteile des Metal Injection Moulding
- Komplexe Geometrien möglich
- Das verarbeitete metallische Material muss nicht aufgeschmolzen werden
- Wirtschaftlichkeit nimmt mit filigranen Strukturen und Schwierigkeit der Nachbearbeitung zu
- Guter Automatisierungsgrad, jedoch erst ab sehr großen Losgrößen wirtschaftlich
Nachteile des Metal Injection Moulding
- Kein Gussprozess, sondern ein Sinterverfahren, somit: viele Prozessschritte, lange Zykluszeiten: 24-36 Stunden für ein Werkstück
- Grünlinge schrumpfen um bis zu 25 % beim Sintern. Daher entstehen häufig Probleme hinsichtlich der Kontinuität der Maßhaltigkeit in einer Serienfertigung
- energieintensiver Prozess des Sinterns
- Relativ selten eingesetztes Verfahren, sodass wenige Daten für stabile und uniforme Prozesse vorhanden sind
- Einschränkung in Gewicht der Werkstücke: eher für sehr kleine Bauteile geeignet, Bauteile mit mittleren Wandstärken weisen extrem lange Sinterzeiten auf
- Zufällige Schwankungen der Metallpulverpartikelgröße kann zu inhomogener Verteilung von Polymerbinder und Metallpulver führen, was Schwachstellen am Endprodukt (Kerbwirkung, Bruchstartpunkte) bedingt
Das Druckgussverfahren ist eines der bedeutsamsten Gießverfahren in der modernen Gießtechnik. Es bietet ideale Voraussetzungen für die wirtschaftliche Herstellung maßgenauer Gussteile von hoher Oberflächenqualität.
Druckgießen ist ein urformendendes Herstellungsverfahren, welches zu der Gruppe der Gussprozesse ohne Modell und dauerhafter Form zählt und sich besonders für Großserien- bis Massenfertigung eignet. Durch Kleinserienformkonzepte sind allerdings inzwischen auch mittlere bis kleine Losgrößen wirtschaftlich herstellbar. Hauptsächlich werden Bauteile aus niederschmelzenden Legierungen wie Zink, Aluminium und Magnesium als Gusswerkstoffe verwendet.
Jedoch gibt es im Zuge der weiterentwickelten Werkstoffe für Druckgussformen inzwischen auch einen signifikanten Anteil an Gussteilen welche bei über 1000°C im Druckgussverfahren hergestellt werden. Insbesondere handelt es sich dabei um Bauteile auf Kupferbasis. Zum Beispiel der Werkstoff Siliziumtombak. Durch das Legieren mit Zink bildet sich ein Mischkristall mit erhöhter Festigkeit aus. Man spricht dann in der Regel von Messing. Es wird auch der Begriff Tombak verwendet, wenn der Kupferanteil bei mindestens 80% liegt. Wenn zusätzlich noch mit Silizium legiert wird, kann eine weitere Festigkeitssteigerung erzielt werden. Die mechanischen Eigenschaften sind dann ähnlich wie bei Edelstahl.
Druckgussteile werden auf Druckgussmaschinen hergestellt. Druckgussmaschinen bestehen aus einer Art Presse mit fester und beweglicher Aufspannplatte, in denen die zwei Druckgussformhälften verbaut sind. Unter extremen Druck (ca. 1000 bar) wird in kurzer Zeit (wenige Millisekunden) das flüssige Metall in die Stahlform geschossen und erstarrt innerhalb weniger Sekunden zum fast fertigen Gussteil. Damit die beiden Formhälften dabei nicht auseinander gesprengt werden, wird die Presse über einen Kniehebel mit bis zu 4000 t mechanisch verriegelt.
Es werden zwei Bauarten unterschieden:
- Warmkammer-Druckgussmaschinen: Bspw. geeignet für Zinkdruckguss. Die Gießeinheit befindet sich dauerhaft in der flüssigen Schmelze.
- Kaltkammer-Druckgussmaschinen: Bspw. geeignet für Aluminium-Druckguss oder Siliziumtombak-Druckguss. Vor jedem Schuss wird die dazu benötigte Menge an flüssigen Material mittels Gießlöffel vom Schmelzofen in die Gießkammer gefüllt.
Im Folgenden ist der Ablauf des Druckgussverfahrens skizziert:
- Schritt 1: Die zwei stählernen Formhälften werden auf einer Druckgussmaschine aufeinander gepresst
- Schritt 2: Metall wird in die Gießkammer gegossen, Gießkolben fährt vor und füllt die Kavität (den Hohlraum in der Stahlform)
- Schritt 3: Form öffnen und Entnahme des Gussbaums (bestehend aus Gussteilen und Angusssystem)
- Schritt 4: Aufbringung von Formschlichte
- Schritt 5: Einfaches und sauberes Trennen der kleinen Anschnitte mittels Stanzwerkzeug
Vorteile des Druckgussverfahrens
- Kurze Zykluszeiten von 8-100 Sekunden, abhängig von der Bauteilgröße
- Sehr geringe Stückpreise möglich
- Hohe Maßgenauigkeit: < 0,05mm
- Geringe Wanddicken möglich (< 1,5mm)
- Glatte Oberflächen
- Hohe Prozesssicherheit und hohe Kontinuität der Maßhaltigkeit, da immer wieder in dieselbe Form aus gehärtetem Stahl gegossen wird.
- Wenig Prozessverluste und Abfälle, umweltfreundliche Gussproduktion
- Near-net-shape Produktion
- Die schnelle Abkühlung beim Druckguss führt zu einer feinen Kornstruktur und damit einhergehend zu besseren mechanischen Werten
Nachteile des Druckgussverfahrens
- Begrenzte Werkstoffauswahl, limitierender Faktor: thermische Beständigkeit der Dauerform
- Einmalige Investitionskosten in ein Druckgusswerkzeug notwendig
- Hinterschneidungen müssen über Schieber in der Druckgussform abgebildet werden
Der Sandguss zählt zu den Urformverfahren mittels verlorener Form und dauerhaften Modell. Mit Hilfe des Verfahrens können metallische Werkstücke hergestellt werden, wobei sich das Werkstückgesicht tendenziell eher im Kilogrammbereich bis zum Tonnenbereich bewegen kann.
Zunächst wird die untere Formhälfte gefertigt. Dazu wird das Modell (früher aus Holz, heute vermehrt aus Polymer oder Aluminium) in den Unterkasten eingelegt und mit Formsand umschüttet. Der Sand wird dann durch Druck und Rütteln verdichtet und anschließend wird das Modell zerstörungsfrei entfernt. Dieselbe Prozedur wird für den Oberkasten durchlaufen.
Danach wird, falls von der Konstruktion verlangt, ein Kern zwischen die Kastenhälften gelegt, die beiden Kastenformen zusammen gefügt und die Schmelze in die fertige Sandform abgegossen. Um das Gussteil nach der Erstarrung freizulegen, muss die Sandform zerstört werden. Das entformte Gussteil muss anschließend noch vom Anguss, jeglichen Steigern und ggf. dem Kern befreit werden.
Im Folgenden ist der Ablauf des Sandgussverfahrens skizziert:
- Schritt 1: permanentes Positivmodell mit Angusssystem wird hergestellt
- Schritt 2: oberer und unterer Formsandkasten wird mit Sand gefüllt und verdichtet
- Schritt 3: Positivmodell wird in die Sandform gedrückt und erzeugt im Sand die Negativkontur
- Schritt 4: keramische Formschlichte wird auf den Sand aufgebracht
- Schritt 5: oberer Formsandkasten wird gewendet und auf den Unterkasten gesetzt, Verriegeln der Formhälften
- Schritt 6: Abgussvorgang mit anschließender Erstarrung
- Schritt 7: Entformung durch Zerstörung der Sandform
- Schritt 8: Formsand in die Sandaufbereitung Transprotieren, Frischsandzugabe
- Schritt 9: Trennen der Anschnitte mit Trennscheibe, Überschleifen der Anschnitte
- Schritt 10: Reinigung des Gussteils von Sandrückständen
Vorteile des Sandgussverfahrens
- Sehr große und voluminöse Werkstücke gießbar
- Klein- bis Großserien rentabel
- Breite Materialpalette an metallischen Werkstoffen können verarbeitet werden
- Trotz verlorener Form gewisser Automatisierungsgrad möglich
- Mäßige Anzahl an Prozessschritten
Nachteile des Sandgussverfahrens
- Raue Oberflächen
- Maßschwankungen um bis zu 5 %
- Wanddicken >3,5 mm notwendig
- Immer mit Nachbearbeitung des Werkstücks verbunden
- Durch den Formsand wird unter unsauberen Bedingungen Produziert, Emission von Gasen
Sandguss ist im Allgemeinen nur für relativ grobe Bauteile mit vergleichsweise großen Toleranzfedern und geringen Anforderungen an die Oberflächengüte geeignet. Die Qualität ist nicht vergleichbar mit Feinguss, MIM oder gar Druckguss.
Vergleich der Verfahren
In folgender Tabelle sind die Stärken und Schwächen der 4 Verfahren dargestellt.
Druckguss | Feinguss | MIM | Sandguss | |
---|---|---|---|---|
Maßgenauigkeit | ++ | + | + | – |
Oberflächengüte | ++ | ++ | + | – |
Wanddicken | ++ | ++ | + | – |
Werkstoffauswahl | / | + | / | + |
Nachbearbeitungsaufwand | + | + | + | – |
Bauteilgröße | + | + | – | ++ |
Stückzahlen | ++ | / | + | + |
Komplexität der Bauteile | + | ++ | + | / |
Zykluszeit | ++ | – | – | / |
Umweltfreundlichkeit | ++ | – | – | – |
Legende: | (Relativbeziehung: sehr gut (++), gut (+), mittelmäßig (/), schlecht (-)) |
In den entscheidenden Kategorien wie Maßgenauigkeit und Oberflächengüte kann mit dem Sandguss in der Regel kein zufriedenstellendes Ergebnis erzielt werden. Das Einsatzgebiet und die Stärken des Sandgusses liegen vor allem in der Herstellung von Gussteilen oberhalb eines Kilogramms.
Der gesonderte Vergleich der konkurrierenden Verfahren Feinguss und MIM mit dem Druckguss dagegen zeigt, dass jeder der drei Prozesse bei der Herstellung filigraner Bauteile individuelle Stärken aufweist.
Die wesentlichen Unterschiede die zu Gunsten des Druckgusses sprechen, sind durch die Tatsache begründet, dass Druckguss…
… im Vergleich zu Feinguss ein Gießprozess in Dauerformen ist und die Gussform somit nicht nach jedem Gießzyklus zerstört und neu aufgebaut werden muss.
… im Vergleich zu MIM kein Sinterverfahren ist. Gießen läuft weitaus schneller ab und die Werkstoffeigenschaften stellen sich aus einer homogenen Schmelze ein.
Wirtschaftlichkeit und Vorteile beim Gießen in Dauerformen (Druckguss): Die Effizienz der Arbeitsweise im Dauerformguss ist deutlich höher als die beim Gießen in verlorene Formen. Aufgrund der besseren Automatisierbarkeit sinkt der Anteil der manuellen Arbeitsgänge. Der Dauerformguss ist im direkten Vergleich mit dem Gießen in verlorene Formen weniger komplex. Auch wirken sich weniger Einflussparameter auf die Gussteilqualität aus.
Dauerformkonzepte werden den Bestrebungen, sorgsam mit den zur Verfügung stehenden Ressourcen umzugehen, insgesamt eher gerecht, als Verfahren mit verlorenen Formen. Die Produktion mit Dauerformen ist sehr viel sauberer:
- geringere Emission von Luftschadstoffen
- deutlich weniger Abfälle bei der Produktion: Beim Sandgussverfahren fallen beispielsweise etwa 500 kg unbrauchbare Sandabfälle pro hergestellter Tonne an Fe-Gusserzeugnissen an.
Dauerformguss stellt – im direkten Vergleich zum Konzept mit verlorenen Formen – insgesamt die umweltfreundlichere Technologie dar.
Fazit
Falls der gewählte Werkstoff des Bauteils im Druckgussverfahren verarbeitet werden kann, sollte dieses Verfahren den anderen hier gezeigten Verfahren vorgezogen werden. Eigenschaften des Druckgussverfahrens:
Effizienz in der Arbeitsweise: Für hohe Wirtschaftlichkeit und Rentabilität
Enge Toleranzen: Die Produktqualität ist gleichbleibend hoch
Sauberes Verfahren: Die umweltfreundliche Technologie der Zukunft
Lediglich wenn der Werkstoff nicht im Druckgussverfahren verarbeitet werden kann, macht die Wahl eines abweichenden Verfahrens Sinn. Dies ist auf den ersten Blick z.B. für den Werkstoff Edelstahl der Fall. Inzwischen gibt es jedoch mit Siliziumtombak eine etablierte Werkstoffalternative, die im Druckgussverfahren verarbeitet werden kann.