Procurement of high-strength and accurate parts
A support to make a decision for CAD designers and technically orientated purchasers.
The following production processes allow the production of high-strength and accurate parts:
- Investment Casting
- Metal Injection Moulding (MIM)
- High Pressure Die Casting
- Sand Casting
Download now for free the construction guideline!
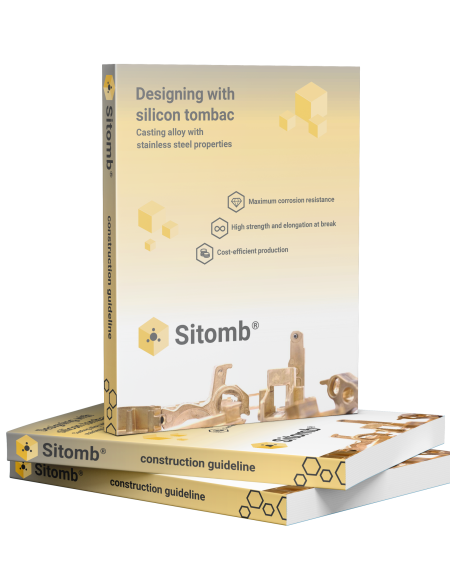
Investment casting, high pressure die casting and sand casting are “casting” methods. There are two different types of casting methods.
Casting in lost moulds:
Lost molds are used in the investment casting and the sand casting methods. As soon as the casting part solidifies the mold gets destroyed so it is possible to take out the cast part. Because mold production is integrated into each individual casting cycle, these processes tend to be costly and have low process reliability (and therefore cannot be automated).
Casting in permanent molds:
In the high pressure die casting method the casting molds are permanent, so the production of the tool is not a part of every production cycle. The whole time the same tool made of tool steel is in utilization. Process reliability, as the basis for automatability and reproducible quality, is significantly increased by casting in the same mold every time.
On the other side the metal injection molding (MIM) method is a sintering process and not a casting process.
While using the high pressure die casting method the strength of the material in utilization is important. In many cases the resulting products of tin and aluminium high pressure die casting do not have enough strength. Unlike alloys based on copper, like silicon tombac, they have similar strength characteristics as parts made of a FE-base. That is the reason why Sitomb is a real alternative to the investment casting and the metal injection molding methods.
Up to a certain point parts made in sand casting will have these characteristics, but usually these parts do not have the required surface quality and tolerance accuracy.
In the following part we compare the characteristics of the four different production processes and identify the advantages and disadvantages of each production process. After that we draw a conclusion.
Procedure
Investment casting, as well known under lost-wax method, is a casting metal-forming technique with lost models and lost molds.
The lost mold is made of ceramic and its main characteristic is that it gets destroyed after every cast to remove the cast part from the mold. Consequently the mold is “lost” every single production cycle.
For the production of a mold a lost model made of wax or polymer is necessary.
In the investment casting method parts are casted which have a high surface quality and a sufficient shape accuracy.
Every metal alloy with flow characteristics which fill the ceramic mold is a possible basic material for the casting process. Commonly steel or stainless steel is in utilization in this process. That is the reason why it is also called steel investment casting and stainless steel investment casting. For the production of the ceramic mould a model made of wax or polymer is necessary.
These models, for example made with an injection moulding machine, have the same measurements as the final metal part (positive model). Normally more than one part is casted in a single cycle. For that reason the wax or polymer model gets connected to a gaiting system (casting pit). In the next the casting pit gets bathed in slurry and sanded afterwards. This process will be repeated until the ceramic layer gets thick enough.
Then the wax or the polymer needs to be removed from the ceramic mold. To do that the mold gets heated up in an autoclave oven. The material in the mold melts and runs out. (Other materials, like foamed polystyrene will be removed by pouring the metallic melt in the mold – Warning: Gas formation leads to qualitative disadvantages.)
After the removal of the model material the burning of the ceramic mold takes place at temperatures above 1000°C. Then the molten metal gets casted in the mold while it is still warm. This process is still manual. Now the material cools down and gets in the requested shape. After the cooling process the ceramic mold gets destroyed to get to the part. Lastly the part gets cut of the casting pit and the sprue gets polished.
In the following the process of the investment casting method is shown step by step:
- Step 1: Production of the lost model (positive model). For medium up to higher quantities this process normally an injection moulding process is in use:
- 1.1 Close the mold
- 1.2 Plastic is melted in an extruder screw, the extruder screw goes forward and fills the cavity
- 1.3 Solidification, opening of the mold
- 1.4 Removal of the casting tree (sprue system and cast parts)
- 1.5 Application of mold coating
- 1.6 Separation of the wax model and the sprue
- Step 2: Wax models getting manually soldered to a gaiting system which is also made of wax
- Step 3: Dip in the wax in ceramic slurry, let the first layer dry
- Step 4: Sprinkling the layer with sand, dipping it again in the ceramic slurry, repeating the cycle of sprinkling and dipping (approx. 10 times)
- Step 5: Burning of the ceramic mold, at the same time the melting wax runs out
- Step 6: Casting the metal in the annealing ceramic mold
- Step 7: Cool down (multiple hours)
- Step 8: Destroying the ceramic mold, removing the casting tree
- Step 9: dispose the broken parts of the ceramic mold
- Step 10: Complex separation of the thick gate from the cast part with a cut-off wheel. The thick gate is necessary, as only the force of the gravity puts pressure on the casted material during the casting process to fill the mold. Afterwards the gate needs to be polished manually.
- Step 11: Cleaning the casting part
Advantages of investment casting
- Suitable for complex parts
- Near-net-shape production
- Possibility to cast parts from one gram to 100 kilograms
- Big variety of metallic materials can be used in the production
Disadvantages of investment casting
- Automation is not possible, results in heavy manual workload
- Long production process and long cycle period
- A lot of waste results from work with lost moulds and models
- Different measurements in the production, as for every single cast part a new model and mould is necessary
The possibility to recycle is in the production process limited because of the lost model and the lost mold. A lot of waste is produced, so the process is bad for the environment and it is also not compatible to the lean-production system in modern manufacturing businesses.
The strength of the investment casting is that it is possible to cast complex parts with numerous indentations. Furthermore it is sometimes commercial efficient to produce small quantities in investment casting.
If there is a need for a product made of steel, investment casting is necessary as well. Since it is not possible to cast steel in high pressure die casting. Otherwise steel would be casted in steel and the result would be that the molds would wear out very quick. As an alternative to stainless steel silicon tombac is commonly in utilization. The advantage of silicon tombac compared to stainless steel is that it is possible to use high pressure die casting. That is a way to get around the commercial and technical processing disadvantages of investment casting.
The metal injection molding method is difficult to compare to the other described methods, since it is no casting method. The final characteristics of the part getting defined in a sintering process.
The basic material for this method is a mixture of metal powder and a binder on a polymer base. This mixture is the feedstock of the MIM process. For the actual production process the pelletized or granulated mixture gets filled in an injection molding machine. There it gets transported, heated and compacted with a doubled worm gear. That is why the binder part of the mixture melts. A thick mass with metallic particles gets casted in an injection mold afterwards. Then the polymer cools down and an instable green body gets out of the mold.
Now the green body has to lose all the binder material. Therefore the green body gets in an oven or in solution bath. That depends on the type of binder, but the most common way to do it nowadays is the oven. The reason is that you do not have to move the green body for the next step of the process. The sintering takes place in the oven as well, you just have to change the parameters of the oven. Afterwards the part losing the remaining binder material, gets in its final shape and mechanic characteristics. Only through the sintering the metal powder particles of the part bind together.
In the following the process of the metal injection molding (MIM) method is shown step by step:
- Step 1: Mixing metal powder and binder
- Step 2: Production of the feedstock by granulating the mixture
- Step 3: Pouring the feedstock in the injection molding machine
- Step 4: Feedstock gets poured in the permanent metallic mold
- Step 5: Opening the mold and taking out the green body
- Step 6: Cutting of the gates
- Step 7: Carful transportation to the debinding system
- Step 8: Sintering process: needs high temperatures (> 1000°C for parts on Fe-Base), much time (>24h) and commonly pressure support
- Step 9: Cooling down of the part
- Step 10: Correction of deforming resulting out of the shrinking process of the green body to become a finished part
Advantages of metal injection moulding
- Suitable for complex parts
- It is not necessary to melt the metal in the process
- Economic efficiency increases when the is structure filigree and the rework is difficult
- High level of automation, commercially efficient just in high quantities
Disadvantages of metal injection moulding
- Since it is a sintering process and not a casting process there are many process steps and long cycle times of 24-36 hours for one part
- The green bodies shrink up to 25% in the sintering process. That is the reason why there are problems with the continuity of the size accuracy in a series production
- The sintering process is energy-intensive
- Rarely used method, so there is not enough data for a stable and uniform process
- Limitations in the weight of the part: better for small parts, since there are long sintering times for parts with medium wall thickness
- The random variations of the size of the metal powder particles can lead to an inhomogeneous distribution of the polymer binder and the metal powder. That results in weaknesses in the finished product (notch effect, breakage point)
The high pressure die casting process is one of the most important casting methods in the modern casting technology. It has perfect requirements for an efficient production of accurate casting parts with a high surface quality.
High pressure die casting is a casting method without a model and a permanent tool. Therefore it is perfect for large series or the mass production. Due to small series concepts it is possible to cast small and medium quantities commercially efficient in high pressure die casting. Normally the parts are made of alloys from zinc, aluminium and magnesium because of the low melting temperatures.
Due to the development of the materials it is possible nowadays to cast parts which are made in high pressure die casting with temperatures above 1000°C. This significant share of casting parts are based on a copper alloy. One example as a material for these copper based alloys is silicon tombac. By alloying with zinc a solid solution with high strength develops. Usually it is called brass, but if the copper share is above 80% it is called tombac. When you additionally alloy with silicon it is possible to achieve an even better strength. The resulting mechanical characteristics are similar to the ones of stainless steel.
Die castings are produced on die casting machines. Die casting machines consist of a type of press with a fixed and moving platen in which the two die halves are installed. Under extreme pressure (approx. 1000 bar) it just takes milliseconds to shoot the liquid metal in the steel tool. There it solidifies in a few seconds and results in a cast part that is nearly finished. High pressure die casting parts are made on high pressure die casting machines. In these machines is a type of press, which consists a steady and an agile fixing plate is. To prevent the tool halves from bursting, the press gets locked by a mechanical toggle lever with 4000t.
There are two different types of high pressure die casting machines:
- Hot-chamber high pressure die casting machine: As an example it is suitable for zinc high pressure die casting. The casting unit is all the time in the liquid melt.
- Cold-chamber high pressure die casting machine: As an example it is suitable for aluminium and silicon tombac high pressure die casting. Before the actual casting process starts the liquid needs to be moved from the melting furnace to the shot chamber with a casting ladle.
In the following the process of the high pressure die casting method is shown step by step:
- Step 1: In the high pressure die casting machine the two halves of the steel tool getting pressed together
- Step 2: Metal is casted in the shot chamber and then a plunger drives forward and fills the cavity in the tool
- Step 3: The tool opens and one is able to take out the casting tree (consists the casting parts and the gaiting system)
- Step 4: Application of mold coating
- Step 5: Clean and easy separation of the small gates with a punching tool
Advantages of high pressure die casting
- Short cycle times of 8-100 seconds, depends on the size of the part
- Really low unit prices are possible
- High dimensional accuracy: < 0,05mm
- Small wall thicknesses are possible (< 1,5mm)
- Smooth surface
- High process reliability and high continuity of the size accuracy, since the same steel tool is the whole time in casting process in utilization
- Little process loss and waste resulting in an environmentally friendly casting production
- Near-net-shape production
- Out of the fast cooling down process in high pressure die casting results a fine grain structure and better mechanical characteristics
Disadvantages of high pressure die casting
- Limited range of materials, limiting parameter: thermal resistance of the permanent tool
- One time investment in a high pressure die casting tool is necessary
- Undercuts need to be displayed by slides in the high pressure die casting tool
Sand casting is a casting metal-forming technique with lost moulds and permanent models. With this method it is possible to cast metal parts. Normally this parts are heavier and bigger. They weight up to many kilograms or even tons.
At first the lower part of the mould is manufactured. Therefore the model (in the past the model was made of timber, nowadays it is polymer or aluminium) is placed in the lower part of the molding box and the box gets filled with molding sand. With pressure and vibration the sand compresses. Afterwards the model gets removed without any damage. The same process happens for the upper part of the mold.
After that the two parts of the mold are joined together and the melt gets casted in the sand mold. If it is necessary for the construction of the part a core has to be placed in the mold before the casting process starts. Then the sand mold has to be destroyed to get to the cast part. Lastly the gates and if necessary the core need to be removed of the demolded cast part.
In the following the process of the sand casting method is shown step by step:
- Step 1: Manufacturing of a permanent positive model with gaiting system
- Step 2: Upper and lower part of the mold getting filled with sand and then the sand gets compressed
- Step 3: By pushing the positive model in the sand mold a negative contour is formed
- Step 4: Application of ceramic mold coating on the sand
- Step 5: Turning around the upper part of the molding box and joining both parts together
- Step 6: Casting process and cool down of the cast part
- Step 7: Demolding by destroying the sand mold
- Step 8: Transport of the old sand to the sand preparation plant, adding new sand
- Step 9: Cutting off and polishing the gates
- Step 10: Cleaning of the casting part to get rid of the rest of the sand
Advantages of sand casting
- Very large and voluminous parts are castable
- Small and large series are profitable
- Big variety of casting materials
- Even with the lost mould an automation is possible to a certain point
- Moderate amount of process steps
Disadvantages of sand casting
- Rough surface
- Dimensional fluctuations of up to 5%
- A minimum of > 3,5mm wall thickness is necessary
- Rework of the cast part is always needed
- Due to the moulding sand the production is unclean, resulting in the emission of gases
Normally sand casting is just used for parts with quite large tolerances and low demands to the surface quality. The quality of the products made in sand casting is not comparable to the products of investment casting, MIM or high pressure die casting.
Comparing the different casting methods
In the following table you can see the strengths and weaknesses of the four different casting methods.
High pressure die casting | Investment casting | MIM | Sand casting | |
---|---|---|---|---|
Dimensional accuracy | ++ | + | + | – |
Surface quality | ++ | ++ | + | – |
Wall thickness | ++ | ++ | + | – |
Variety of materials | / | + | / | + |
Rework | + | + | + | – |
Size of the part | + | + | – | ++ |
Quantities | ++ | / | + | + |
Complex parts | + | ++ | + | / |
Cycle time | ++ | – | – | / |
Enviromental sustainability | ++ | – | – | – |
Legend: | (excellent (++), good (+), average (/), bad (-)) |
In the most important categories, size accuracy and surface quality, the results of sand casting are not satisfying. The utilization and strength of sand casting lie in the production of parts heavier than one kilogram.
The comparison between the investment casting, MIM and high pressure die casting shows that every method has its own individual strength in the production of filigree parts.
The main differences that speak for the usage of high pressure die casting are the facts that:
High pressure die casting is compared to investment casting a process with a permanent mold, so it is not necessary to destroy the mold and build a new one every single casting cycle.
By using high pressure die casting and not MIM there is no sintering process needed. The casting process is faster and characteristics of the part result out of a homogeneous melt.
Economic efficiency and advantages of casting in permanent molds (high pressure die casting): The efficiency of working with permanent molds is higher than with lost molds. Due to the better automation the amount of manual process steps is lower, so the whole casting process is less complex. Furthermore there are less parameter who have an influence on the casting quality.
Concepts with a permanent mold are compared to casting processes with a lost mold more resource saving, so that the production with a permanent mold is cleaner and fits to a modern corporate image:
- Lower emission of air pollutants
- Significant lower amount of waste in the production: For example results out of the production of one ton of Fe-castings in sand casting 500 kg of unusable sand waste.
In total the production with permanent mould is compared to the production with lost moulds the more environmentally friendly technology.
Conclusion
If the chosen material for the part is castable in high pressure die casting, then high pressure die casting should be used instead of the other methods. Characteristics of high pressure die casting:
Efficient production: High economic efficiency and profitability
Low tolerances: The product quality is continuously high
Clean method: Environmentally friendly technology
The utilization of a different method just makes sense, if the material is not castable in high pressure die casting. One example is stainless steel. Nowadays there is an alternative in silicon tombac, which is castable in high pressure die casting.