Sitomb® – Silicon tombac die casting
Sitomb® is the new construction alloy for highly-stressed and accurate components. Its characteristics are similar to stainless steel. With one distinct advantage: Sitomb® can be processed using the economical die casting process. This is not possible with stainless steel. Castings made of stainless steel need to be processed using the more complicated investment casting procedure.

Maximum corrosion resistance
Sitomb® workpieces are particularly resistant to corrosion due to the high copper content of 80%*.
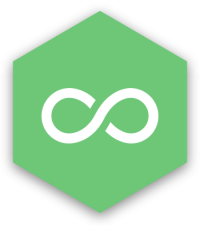
High strength and elongation at break
Strength properties up to 700 MPa are possible. In any case a minimum of 500 MPa is guaranteed. Despite this excellent strength characteristic, high elongation values of >10% are reached before the part breaks.

Cost-efficient production
Using the high pressure die casting method for our production allows us to produce more parts per time unit compared to other methods. Hence, we reach low unit costs.
*More detailed technical information on Sitomb® can be found in our design guidelines.
When is Sitomb® used?
Mainly in these situations:
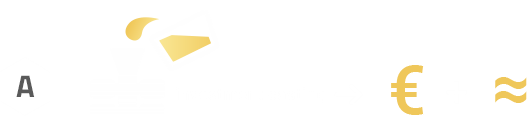
Parts resulting from steel investment casting are too inaccurate or expensive

Parts resulting from Metal Injection Moulding (MIM) are too inaccurate, expensive or brittle

Parts resulting from zinc alloy die casting reach too low levels on strength and break in the long-term

The corrosion resistance of the existing detail is insufficient
Other reasons for the use
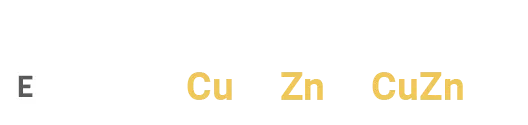
The brass that is used is too soft

Slip properties have to be improved

Antibacterial characteristics are required
Silicon tombac – Sitomb®
Sitomb® is the result from decades of alloy development and process improvement at BREUCKMANN. With specific limitations in the tolerance range for alloy elements of silicon tombac complying with DIN EN 1982 (2.0492.05, C87800, CC761S) and targeted micro alloying, we were able to achieve the metallurgical optimum for our characteristics.
To produce Sitomb®, brass is mixed with silicon and then cooled extremely quickly. At high temperatures around 1000°C silicon is able to move freely within the metal lattice. As soon as the metal cools down to room temperature, the silicon atoms get stuck in specific positions within the interstitial metal lattice. Subsequently, they tense up the structure which results in higher hardness and strength of the component.
A similar behavior can be observed when carbon is added to steel.


The fast solidification leads to a fine grain structure having good mechanical characteristics. Additionally, using silicon for alloys results in an unusual behavior during the local extension when cooling down (avoidance/reduction of casting porosities).
How can I order my customized part made of Sitomb®?


1.) Prototypes:
To get a first impression of our material, you can order a customized prototype online. We refer to this process as “rapid Sitomb®“. It enables you to order first samples without the initial investment of a die casting tool.

Click here, upload your 3D-data online and instantly receive the unit piece. You are able to order directly online.
2.) Series production:
Series production with Sitomb®
